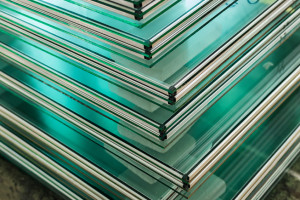
Glass is typically translucent or transparent. The brittle substance is a fusion of soda, lime, sand, and other elements. The most common glass-forming processes use heat to transform raw materials into molten liquid. The mixture is then quickly cooled to create hardened glass.
Properties of Glass Materials
The five primary properties of glass are listed below:
Thermal Properties
It is crucial to consider the desired operating temperature of an application and how it could affect the thermal properties of glass materials. When the temperature dramatically changes, glass can easily shatter and break.
Heat tempering can make glass stronger and minimize thermal shock resistance. The color of glass and tempered glass can also change based on the material’s thermal properties.
Thermal Expansion
When glass gets heated, it expands. Glass with a lower coefficient of thermal expansion (CTE) can be more difficult to shape or distort. Glass materials need to have matching thermal expansion rates to avoid fracture.
Optical Properties
The Refractive Index determines how fast light (electromagnetic waves) travels through glass, allowing engineers to select the correct glass material for an application.
Some factors to consider include:
- Transparency
- UV Transmission
- Optical Needs
Chemical Properties
Most glass materials contain the following elements, with thousands of compositions used to make glass:
- Fluxes
- Formers
- Stabilizers
All soda lime glasses (and some borosilicate glasses) contain sodium or alkali metal ions. These materials can experience leaching when exposed to liquids or vapor. Certain coatings can be used to increase chemical resistance and protect the material.
Electrical Properties
Coated glass can offer varying degrees of conductivity when used with lasers, semiconductors, solar energy converters, and electronic devices.
The following characteristics come into play when evaluating glass materials for use in electronic applications:
- Resistivity
- Composition Changes
- AC / DC Conductivity
- Dielectric Constant
- Electrical Modulus
- Dielectric Loss
Mechanical Properties
The following factors contribute to the evaluation of mechanical properties:
- Strength
- Hardness
- Impact Resistance
- Abrasion
- Viscosity
These factors can be tested to determine the amount of stress a glass material can withstand.
Glass Material Applications
Glass is used as a primary source material in an extremely broad range of industries. The following is a list of some common glass material applications:
- Semiconductor Industry. Glass is vital to the production of semiconductor wafers. Glass wafers act as a carrier substrate, facilitating the safe handling of thinner and more delicate silicone materials.
- Consumer Appliances. Oven doors and stove tops are typically comprised of glass material.
- Biotechnology. The biotech sector relies on borosilicate glass wafers for a variety of medical devices because of its clear optical transparency and resistance to high temperatures, radiation, and energy. Glass wafers also act as a carrier substrate to protect silicone devices used in nanotechnology.
- MEMs and Electronics. TV, computer, and smartphone screens are all made from glass. Engineers use special glass types for touchscreen displays. Glass wafers are also used as substrate carriers and wafer packaging for sensitive components in microelectronic mechanical systems (MEMs) and electronics.
- Automotive and transportation. Windshields, headlights, and backlights make use of specific glass materials. Glass is also used as a source material for many lightweight, reinforced structural components found in automobiles, airliners, helicopters, ocean cruisers, and other vehicles.
- Medical technology. As an example of the use of glass in the medical field, X-ray machines contain glass.
- Renewable energy. Low-iron or extra-clear glass has extremely limited light reflection properties, which makes it an excellent fit for solar cell covers. Maximum amounts of sunlight can come through the glass cover and help charge the solar battery.
- Integrated Circuit (IC) Packaging. Glass vias (TGV) and wafer-level glass capping (WLC) are used to ICs against corrosion or impacts to ensure optimal functionality. They serve a dual purpose of holding contacts to external circuits in place.
FAQ: Properties of Glass
Partnering with Swift Glass for Premium Glass Solutions
For nearly 100 years, Swift Glass has been a worldwide leading manufacturer of quality fabricated glass materials. Swift Glass is an industry leader in glass fabrication. We stock materials from glass manufacturers such as:
- Corning
- GE
- SCHOTT
- Vitro
Each material we stock is carefully selected for its physical properties and unique performance capabilities. We continually update our product offerings to meet the needs of clients across sectors.
Contact Swift Glass today for expert advice. Consulting an experienced glass supplier can help you identify the optimal glass type for your industrial needs.