The Key Differences Between Transmission & Transmittance and How to Apply Them to your Application
Leave a CommentFrom magnifying glasses to tinted windows to one-way mirrors, people prize glass for its ability to transmit (or not transmit) light.
Measuring light transmission and transmittance plays a huge role in selecting an appropriate type of glass for your needs. Transmittance measures the amount of light able to pass through a material without the material reflecting or absorbing it. Therefore, transparent glass will transmit 100% of light, translucent material only allows some light to come through, and opaque glass will achieve close to 0% transmittance.
A few key differences exist between light transmission and transmittance. Understanding the distinction between these two terms will help you select the perfect type of glass for your application.
Transmission vs. Transmittance
Transmission refers to the amount of incident light that successfully passes through glass or other material, and it’s usually expressed as a percentage of light that made it through the material. On the other hand, transmittance refers to the amount of light that a material disperses, effectively resulting in an inverse value of that found for transmission.
There are two basic types of transmission—external and internal—and both differ from light transmittance:
- External transmission is calculated from the intensity of the incident light as it enters the glass versus the light’s intensity after exiting the glass. This transmission measurement technique provides an accurate figure of the actual amount of light allowed to pass through a material.
- Internal transmission is determined by the light’s intensity once it has entered the glass versus its intensity after it leaves the glass. Internal transmission primarily measures the light filtration ability of the glass itself, allowing you to get a more accurate idea of the glass’s properties.
- Transmittance refers to the amount of light energy that the glass absorbs, scatters, or reflects. It’s measured using the formula T = I/I0, with T denoting the transmission intensity, I indicating intensity, and I0 indicating intensity at the start. This calculation allows you to determine the ratio of transmitted radiant power to incident radiant power, giving a greater idea of a glass’s ability to block photons.
How Does Transmittance Apply to My Application?
Transmittance values can vary based on which application or common industry nomenclature they use.
For example, while most manufacturers measure industrial glasses in terms of external transmittance, they usually measure filter glasses in internal transmittance. This is because manufacturers can put an anti-reflective (AR) coating on the glass’s surface, reducing the amount of light intensity lost to reflection.
A couple of common applications that measure transmission include:
- Testing window tint or films for cars, homes, and businesses. Desired tint levels will correspond with the amount of light the glass transmits.
- Measuring glass clarity. Many industries have stringent specifications governing the use of glass in assembly regarding both external or internal transmission. For instance, FAA specifications for airport and aerospace applications typically govern the product’s external transmission potential.
It’s also good to keep in mind that engineers who design optics for extreme environments must recognize that each type of glass will have slight variations in chemical, thermal, and mechanical properties, all of which factor into their ability to reflect and absorb light.
Glass for All Occasions at Swift Glass
At Swift Glass, we pride ourselves on having delivered industry-leading custom glass manufacturing services for almost 100 years to OEMs across the country. Our experience and dedication to customer success enables us to understand our customers’ intricate needs and exceed their expectations.
We’re an ITAR-registered, ISO 9001:2015–certified company and a worldwide leader in fabricated glass parts. We offer holistic assistance in glass crafting, material selection, and custom design, maintaining a high standard of precision and quality.
To learn more about the optical properties of glass, download our latest eBook here, and don’t hesitate to contact us today if you have any questions.
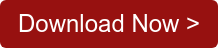
Low-Iron Glass vs. Standard Clear Glass
Leave a CommentThe differences between low-iron and traditional clear glass are pronounced enough that many people can’t believe what they’re seeing – or what they haven’t been – when they’re shown low-iron glass options. Traditional clear glass can be hazy and is often faintly tinted, even at its best. Color issues may arise on the edges of thicker pieces and light often isn’t allowed to truly penetrate the glass due to its chemical makeup.
Conversely, low-iron glass offers a practical solution to common problems associated with traditional clear glass. Glass that is specially manufactured to have a low iron content can shed the bulk of the color casting (tinting) that comes along with traditional glassmaking methods. This lack of color provides exceptional clarity and top-notch light transmission.
What Is Low-Iron Glass?
Low-iron glass, also known as optically clear glass, is made from silica and contains very low amounts of iron. The low iron levels serve to remove the blueish tint that’s associated with thicker traditional glass. Low-iron glass sees wide use in solar applications and is also popular in the aquarium and display industries, where clarity is valued.
Low-iron glass usually has a ferric oxide content about ten times less than ordinary plate glass. Iron is intentionally lowered through the use of special silica sand with naturally low iron levels. This low iron content is what provides the glass with exceptional color neutrality and clarity.
Low-Iron Glass vs. Standard Clear Glass
Iron Content
Traditional glass typically has a ferric oxide content of close to 0.1%. This oxide is one of three key iron oxides of iron.
Manufacturers have managed to get ferric oxide levels down to just 0.01% in low-iron glass.
Color Tint
Standard clear glass’s higher iron content means that it has a blue-green tinge. For those looking to back-paint or coat their glass, low-iron options should not be overlooked. The green hues associated with traditional clear glass can become problematic in terms of aesthetic appeal, as the edges of thicker pieces of glass can often times appear nearly black, creating both an eyesore and color problems. This can create conflicting color problems when painting.
Low-iron glass boasts virtually no color tint. It offers individuals and businesses alike the opportunity to color-match their glass and ensure that it remains aesthetically pleasing. A clearer starting point means less work with color-matching when you need to paint your glass. While even low-iron products will continue to have a hint of color to them, it has been found that smaller pieces will generally exhibit far less tint than larger ones.
Light Transmission
Light transparency can be improved by up to 6% simply through the modification of iron content in glass. Low-iron glass provides maximum brightness and clarity with a higher visible light transmittance than traditional clear glass. Applications requiring an unrestricted view can see tremendous improvement with the use of low-iron glass over more traditional options. Low-iron glass achieves these optimum levels of clarity thanks to its iron levels; light transmission levels will virtually never dip below 90% with low-iron glass.
Light transmission is not perfect in low-iron glass, though thinner cuts of low-iron glass will boast more impressive light transmission levels than those that are thicker. One should also consider that between two cuts identical in thickness; however, low-iron glass will always win out over traditional clear glass in terms of light transmission.
Low-Iron Glass Solutions from Swift Glass
At Swift Glass, our experts will guide you through the process of selecting an appropriate low-iron glass solution for your home or your business. For a wide range of applications, low-iron options are the superior choice for those in need of clarity.
If you’re interested in incorporating low-iron glass into your personal or business endeavors, feel free to contact us for more information or to learn more about our optical display glass materials.
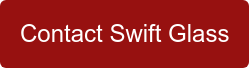